Core Values
RPM was founded on four basic principles: Safety, Quality, Production, and Profit. We embrace these core values in our employees, workplace culture, and customer relationships.
Safety –
“Safety is our number one priority. There is no job we have ever done nor will we ever do that is worth someone getting hurt over. Quite frankly, as far as we are concerned, that job does not exist”
-Robert P Mudge President and Founder
Quality – “The best is barely good enough” RPM is focused on producing the best solution / product at the most cost-effective price for the customer
Production – RPM’s Team utilizes specialized equipment, automation & controls along with a professional work ethic
Profit – When the first three values of Safety, Quality, and Production are embraced, a reasonable profit follows
Mission
RPM & Associates provides the highest-quality manufactured solutions to valued power, mining, and other diverse customers, while striving to help them reduce their operational life-cycle costs. RPM’s most important resource, our innovative employees, have the opportunity for both personal and professional growth while ensuring RPM remains a world-class problem solver! For RPM, “Being the Best is Barely Good Enough!”
Company Timeline
RPM Thinks Green
Fume Generation
RPM’s primary focus is always on Safety. Hardface Welding Practices produce fumes containing hexavalent chromium. Regardless of whether RPM is welding at a customers site or in RPM’s facility, generated weld fume is captured by a collection and filtration system. The captured dust is then treated, thus converting the hexavalent chrome to a stable valence state. The converted dust is then properly disposed of in the local landfill or recycled, versus disposing at a hazardous waste facility.
Strategic Metal Conservation
RPM understands that Chromium is a National Strategic Metal that must be conserved, as US Chromium reserves are only 10-12% of annual consumption. The United States imports the remaining 88-90% from countries that are not political friends. RPM’s Steel Core Pulverizer Rolls requires less chrome to produce and rebuild. RPM’s engineered overlay provides extended wear life versus other types of rolls produced, resulting in less chrome emitted into customers combustion gases.
In The Community
Free Wheelchair Mission
RPM & Associates teamed up with the South Dakota School of Mines & Technology to design, test, and manufacture a wheelchair durability testing track for the Free Wheelchair Mission. The Free Wheelchair Mission is a humanitarian, faith-based nonprofit organization that designs and manufactures cost-efficient, durable wheelchairs for developing countries around the world. Data acquired since 2019 has resulted in design changes that have increased the expected life of the wheelchair by over 20 times, with minimal additional cost. To view a video of the testing track in action Click Here.
To learn more: www.freewheelchairmission.org
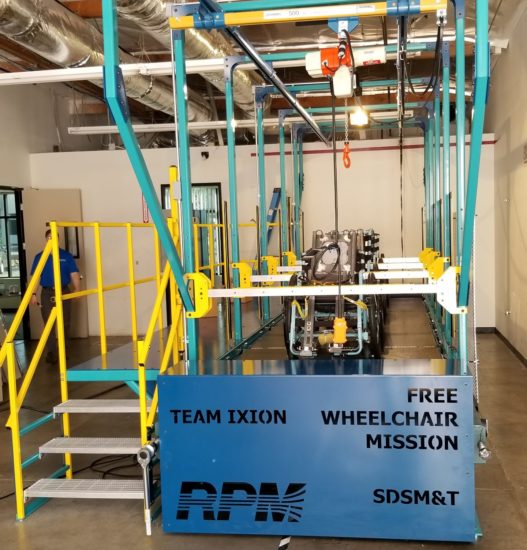
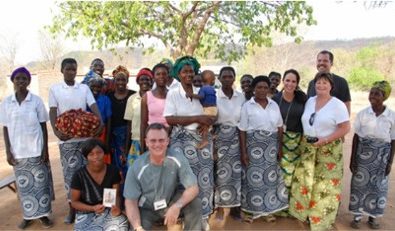
World Vision
RPM & Associates founders Rob & Deb Mudge are longtime supporters of World Vision. World Vision is a Christian humanitarian organization helping children, families, and their communities overcome poverty and injustice.
To learn more: www.worldvision.org